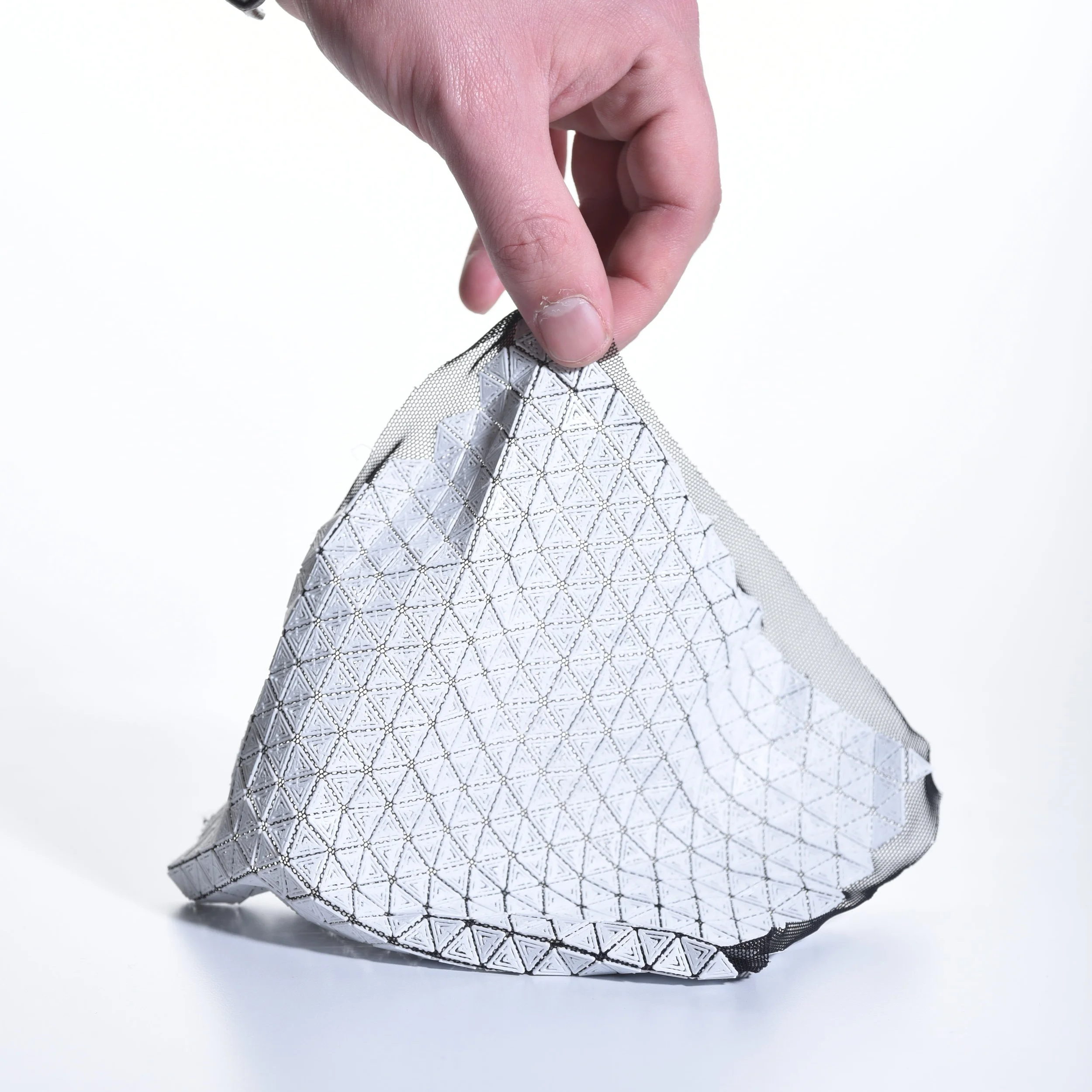
Integrating textile and 3D printing fabrication processes to develop adaptable surfaces for architectural applications
An area of personal interest is the development of digital fabrication tools and the possibilities that come from them. While a student at Jefferson University I had an opportunity to explore applications of 3D printing in relation to architecture. We have already seen advancement in the abilities of large-scale printers using concrete extrusion to build houses, my interest in this field leaned into the idea of rapid-prototyping and form generation.
While exploring applications of digital fabrication, I collaborated with students from the textiles department and developed a method to replicate simple forms created in digital space by using elastic 3D printing filament and a mesh fabric held under tension.
Initially I worked to build a parametric system that allowed the conversion of simple 3D forms created with modulated surfaces into structural guide lines that could be flattened into a 2 dimensional pattern. This pattern was then printed onto a mesh fabric held under tension across the build-plate using an elastic filament to provide a flexible structure to the fabric. When released from tension after the print was complete the pattern of semi-flexible filament forced the fabric to take the shape that was intended.
As a test for application I chose to explore the possibilities of using this generation method to create complex forms for concrete. Using a polyacrylic resin the mesh was hardened and sealed then filled with concrete and allowed to set. Unlike traditional methods of wood or metal form building, this process allowed for the creation of complex form-making with far less material and time. As a proof of concept this application was proven as a potential application of digital fabrication in the field of architecture & construction.